私は金型の製作に長年携わっています。
研削加工・W/E加工・金型仕上げ・成形・金型設計・営業と様々な業務をこなしてきました。W/E工程以外は、グループリーダー・次長・部長と管理業務も行い新しい取り組みにもすすんで取り組んでいます。
まあ、いわゆる職人というぶるいに入っる思っています。現在は技術と営業部のマネージャーの2足の草鞋を履きながら後進の指導にあたっています。金型業界が海外展開で縮小するなか、経験則から生かせる金型の要点を持論で説明していきます。
金型とは
金型とは製品を作る為の型です。
分かり安い例としては、アイスを作るプラスチックの型などが100均等で良く売られていると思います。
アイスの型にジュース等を入れて冷凍庫で固まるまで待つとアイスが出来上がります
ここでは射出成型金型について私見をいれなががら説明したいと思います。
1.プラスチック射出成形金型とは
プラスチック金型を用いた射出成形は、現状では大量生産に適した生産方式です。また、自動車の内装・電装、家電製品等さまざまな製品があり、製品設計を行う際はプラスチックや金型の知識が必要になります。
1.-1 プラスチック射出金型で
射出成形とは、溶かしたプラスチック材料を金型へ流し込み、冷却させた後に、金型から取り出して製品を取り出します。
射出成形は4ステップでプラスチック製品が出来上がります。
- 型締め
- プラスチック材料を金型に流す・保圧をかける。
- 成形品の冷却
- 型開き、成形品の取り出し
射出成形機は金型を取り付ける部分とプラスチックを型に流す射出部分から構成されています。
射出成形機は金型を閉じプラスチックを溶かして金型に流し込み、金型に流れたプラスチック(成形材料)を冷却して固まった成形品を金型を開いて後に突出して取り出すという機械です。
1-2. プラスチック成形とは
プラスチックの成形では、良品を(表面に傷、凹凸、気泡、バリ、色ムラなど表面不具合の無い)成形するために、射出成形機による成形条件、金型に対しての精度管理等、さまざまな条件設定を行う必要がある。
成形するプラスチック材料には、さまざまな種類が存在します。プラスチックによって溶ける温度が異なるため、「射出成形機のノズル温度(樹脂温)」、「金型の温度」、「射出する速度」、「射出圧力」、などの細かな成形条件設定が必要となります。また、これらの条件によって、成形品の外観が影響するだけでなく、その製品の機械特性にも影響を及ぼします。
また、使用するプラスチック材料のよって製作する金型の設定も変え必要が有る為使用するプラスチック材料の特性を理解する必要があります。
射出成形は製品を大量に生産することができますが、成形条件及び金型の状態によってその品質に影響を及ぼすため、品質管理の実施や品質基準の遵守、適切なプロセス制御と監視が必要になります。製造プロセス全体で品質を管理し、顧客の要求や規格に準拠することが重要です。
1-2-1一般的な成形条件
- 射出速度(Injection Speed): 射出成形機から金型内に材料を射出する速度を制御します。適切な射出速度は、材料の充填性と圧力分布を制御し、均一な充填を実現します。
- 射出圧力(Injection Pressure): 材料を金型内に射出する際の圧力を制御します。適切な射出圧力は、材料の充填性と圧力分布を制御し、欠陥や不均一な充填を防ぎます。
- 保圧時間(Holding Time): 射出が完了した後、金型内の材料を一定時間保圧する時間を設定します。保圧時間によって材料の冷却と固化が促進され、製品の寸法安定性や品質が向上します。
- 保圧(Holding Pressure): 保圧時間中に金型内の材料を保持するための圧力を制御します。適切な保圧圧力は、材料の冷却と固化を促進し、成形品の収縮や歪みを最小限に抑えます。
- 冷却時間(Cooling Time): 成形品が金型内で冷却される時間を設定します。適切な冷却時間は、材料の固化と収縮を完了させ、製品の寸法安定性を確保します。
- 金型温度(Mold Temperature): 金型の温度を制御します。金型温度は材料の冷却速度と製品の品質に直接影響を与えます。適切な金型温度設定は、製品の寸法安定性と表面品質を向上させます。
- 材料乾燥(Drying): プラスチック材料に含まれる水分を除去するために、材料を事前に乾燥させる必要があります。乾燥条件は材料の種類によって異なります。
成形条件は成形技術者が製の状態を確認しながら最適な条件に設定します。
これらの成形条件は、製品の要件や材料の特性に応じて変化する為、記録しておく必要があります。成形条件は、温度環境・成形機の変更・金型の改良等様々な内容の影響を受けますので、常に管理・監視が必要になります。
2. 金型の構造
プラスチック用の金型構造は大きく2つのタイプが存在します。
・2プレート金型
・3プレート金型
2プレート金型は、「射出成形機に固定される固定側」と「金型開閉時に稼働する可動型」の2つに分割される金型です。
3プレート金型は、固定側と可動側に加えて、中間部に「ストリッパープレート」が存在し、金型開閉時には3つに分割される金型で、ランナーが成形機に固定されている板とストリッパープレートの間にあるものと、固定側に分割起工をもうける先抜き構造があります。
まずは、基本的な2プレート金型についての基本的な名称と用途を説明します。
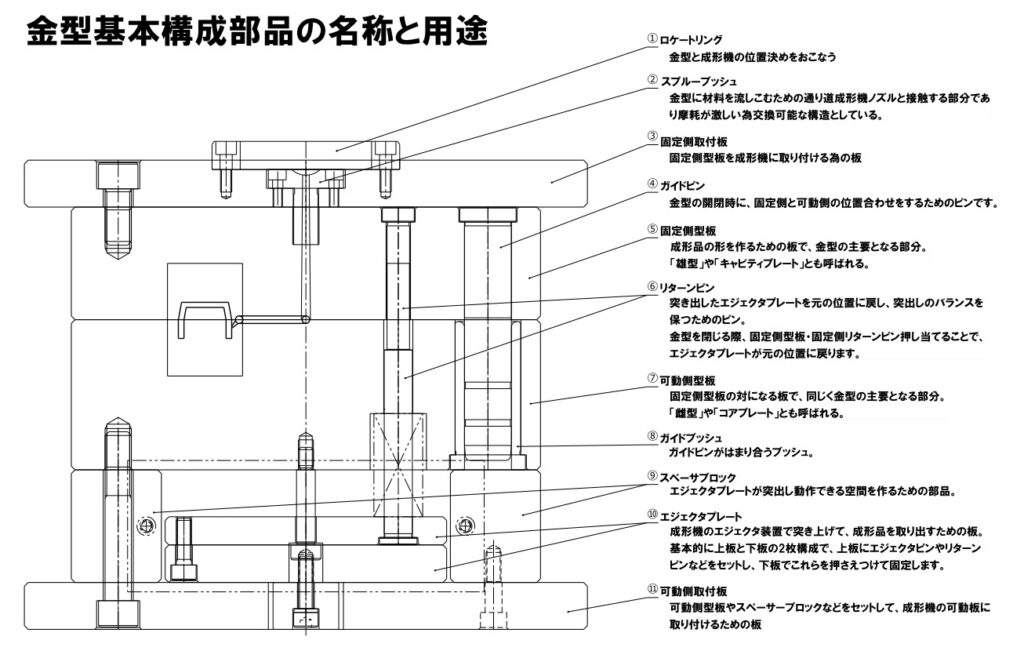
3. 金型のキャビティとコア
金型は成形品を囲んで凸部と凹部に分割されます。
⚫ 凹部はコア(Core)(可動側)
⚫ 凹部はキャビティ(Cavity)(固定側 )
と呼びます。また、コアを雄型 キャビティを雌型ともいいます。
この2つの金型部品は金型を構成するうえで最も重要な部品となります。
元々キャビティは、「空洞」という意味があることから,樹脂が充填される空洞部分のことを指す場合もあります。金型業者はよく「キャビティ」と空洞部分の事を言っていることがありますので、その場の状況から推測することが必要です。
※短縮して「キャビ」と言うことが一般的です。
キャビティ とコア が合わさってできた空洞部に、プラスチックを注入することで空洞部の形をした成形品が出来上がります。
キャビティ(凹部)は、一般的に成形品の外観を形成する形状となることが一般てきです。
キャビティ(凹部)には、金型から成形品が取り出しやすいように傾斜とつけて設計します。傾斜が無い場合成形品がキャビティ側に残り金型が開いた瞬間に、キャビ側に張り付いたままになる不具合となることがあります。キャビ側に貼りついた状態では成形品を取り出すことはできません。
本来、金型が開くと、成形品はコアに貼り付きます。金型が完全に開いた後に、コア側にある成形品を押し出しピンにより金型から押し出され成形品が取り出されます。従って、射出成形機へ金型を取り付ける場合、必ずキャビティが固定側となり、コアが可動側となります。
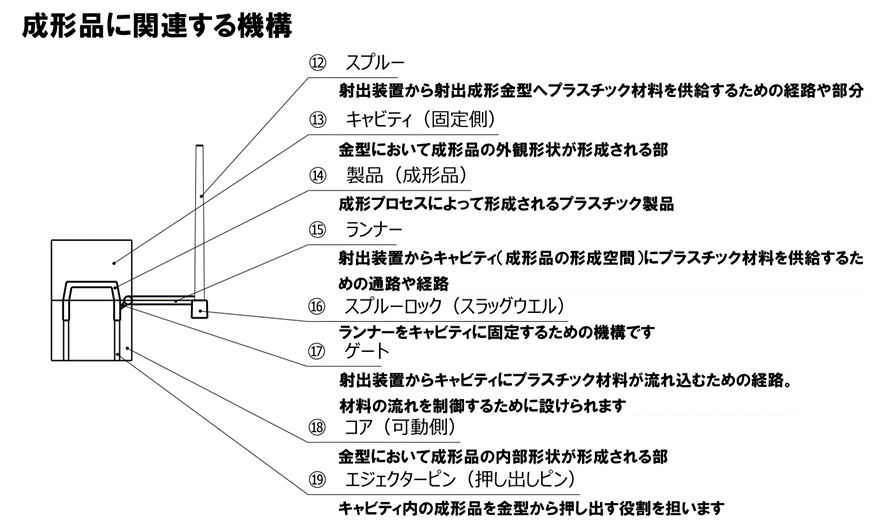
4. スプルー・ランナー・ゲートの機能
金型にプラスチック材料を流すときキャビティとコアにたどり着くまでに3種類の通路を通り充填されることで成形品となります。この3種類の通路にはそれぞれ役割をもっています。
- スプルー
- ランナー
- ゲート
それぞれの役割について説明します。
4-1. スプルー
プラスチック材料を金型に流す際に最初に通る通路となります。
また、スプルーの形状や寸法は、プラスチック材料の充填効果に影響を与えます。設計者の意図によって、プラスチック材料の流れを制御し、成形品内への均一な充填や気泡の排出を促すことができます。
スプルーの断面形状は円形であり、側面には傾斜がつきます。
スプルーは射出装置のから金型のパーティングラインまでの通路を担いますので固定側の金型の厚み分だけ長さが必要となります。
4-2. ランナー
ランナーは射出装置からキャビティにプラスチック材料を供給する通路です。プラスチック材料は射出装置からスプルーを通り2番目に通る通路となります。
また成形品が2つ以上の場合には、ランナーで分岐してそれぞれの成形品への経路となります。
ランナーの形状や寸法は、プラスチック材料の充填効果に影響を与えます。プラスチック材料がキャビティに均一に充填されるように考慮して成形品のバラツキによる欠陥や不均一な厚さの発生を抑えることができます。
ランナーはプラスチック材料が流れる経路であり、冷却効果にも影響を与えます。ランナーの形状や配置によって、プラスチック材料の冷却速度を制御し、成形品の冷却時間や品質を調整することができます。
一般的にはランナーの大きさは成形品の肉厚より太くしなければなりません。
またランナーは大きく分けて「コールドランナー」と「ホットランナー」の2つに大別されます。
4-2-1コールドランナー
コールドランナーは3個以上の多数固取の金型を製作する際は、製品を対称かつ製品までのランナーの距離を同一に設定する必要があります。
ランナー配置のレイアウトが非常に重要になります。
プラスチック材料が製品にたどり着いて充填するまでの時間・圧力がバラバラであった場合には、成形品が同一寸法にならない等の具合が発生します。
このような場合はランナーの太さ分岐までの距離等を調整し製品に均等に樹脂が充填する様にします。プラスチッ材料が製品に均一に充填しているかを確認するための基準としてのゲートバランスを概ね97%以上とする事でバラツキのない成形品を作ることが出来るようになります。
また、ランナーの分岐部分には、コールドスラッグウエルと言われる樹脂溜まり部を設けます、これは最初に金型に入ってきた冷えかかった樹脂を溜めるスポットとなります。
コールドスラッグウエルがないと冷えた樹脂が成形品に流れて、ウエルドラインなどの成形不具合に不具合となります。
コールドスラッグウエルはスプルーとランナーの分岐にも設置します。コールドスラッグウエルの大きさはランナー径の2倍程度にする事が有効となります。
また、下記に示すものがホットランナーとなります。
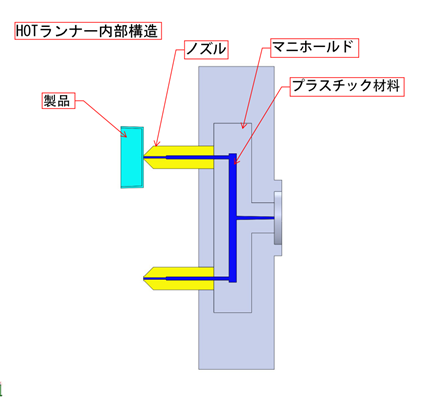
4-2-2ホットランナー
ホットランナーとはコールドランナーと違い製品に直接プラスチッ材料を流す(射出する)システムとなります。
スプルーとランナーが無い事で、プラスチック材料の無駄をなくせる事とゲートバランスを考慮する必要がないことがメリットとなります。
デメリットとして初期費用が高額になることが挙げられます。
4-3. ゲート
ランナーは射出装置からキャビティにプラスチック材料を供給する通路です。プラスチック材料は射出装置からスプルー・ランナーを通り最後に通る通路となります。
ゲートは成形品への入り口です。
ゲートはプラスチック材料の流れ(速度)を制御するために設けられます。ゲートの大きさを小さくすると、速度が上がります。
ゲートの形状や寸法は、プラスチック材料の充填効果に影響を与えます。
また、速度が早すぎた場合、ジェッティングといってプラスチック材料が高速でキャビティ内に流れ、突然方向を変えて急速に冷却されることによって起こります。
成形品にプラスチックが勢い良く流れた模様が表面に現れます。
そのほか、フローマークといって、ゲートを通過したプラスチックが縞模様のよう
に現れる現象があります。
速度が遅い場合におこります。プラスチック材料が金型表面の接触する際に起こる冷却効果の違いが影響しています。
その為、綺麗な成形品を造るには最適速度で製品部に流れるように、スプルー・ランナー・ゲートを設定する必要があり金型設計のノウハウとされます。
ゲートについては成形品の表面に跡が残ることから、製品設計者はゲートの形状や位置を想定して設計する必要があります。
ゲートにも様々な種類があり
一般的に
- サイドゲート
- サブマリンゲート
- バナナゲート
- ピンゲート
- ダイレクトゲート
などガあります。
4-3-1サイドゲート
成形品の横のパーティングラインと同じ位置で設置します。
ゲートのサイズを大きく設定できる特徴があり圧力がかかりやすいゲートとなります。
4-3-2サブマリンゲート
トンネルゲートともいわれパーティングラインから製品に潜り込んで設置されます。
射出成型時、金型が開く際に成形品からゲートカットされるのが特徴です。
4-3-3バナナゲート
パーティングラインより潜り込んで製品の裏側(下面)に設置されます。
成形品の側面や天面にゲートの跡が残ってはいけない場合等に使用されることがあります。(一般的にはあまり使用頻度は高くないです。
4-3-4ピンゲート
3プレート金型で使用されます。成形品天面に設置します。
小型、肉薄の製品に向いており、ゲート跡が小さい為ゲート跡があまり目立たない特徴があります。
4-3-5ダイレクトゲート
ランナーなく直接製品にゲートを作ります。 ホットランナーシステム等がそれにあたります。
以上、金型製作の経験から記載した内容となります。
私見がはいいている為一部内容に誤りがあるかしれませんので参考としてください。
そのうち、金型製作における製品について書きたいと思っています。
コメント