金型設計とは、製品を成形・加工するための道具である金型を設計する業務スです。金型は、プラスチック成形、金属加工、ガラス製造など、さまざまな産業で使用される重要なものです。金型設計とは、製品の形状や寸法を考慮して規格どうりの製品を量産するための金型を製作するための部品図等の設計を行うことをいいます。
金型設計手順
金型設計を始める前に、製品の情報を取得ます。
製作する製品の形状、重要な寸法、コネクタ等であれば勘合する製品の情報インサートする端子の情報などさま様な情報を入手する必要があります。
- 製品の形状から、肉薄部、肉厚部、勘合部、ロック形状等の情報を分析し金型として成立する形状かを確認します。
- 肉薄部はへの樹脂流動を考慮したうえで、充填はしっかり行われるか変形及び強度の不安は無いかと検討します。
- 肉厚部は、樹脂の冷却効果により変形・ヒケの発生は懸念されます異常変形が想定されますので、対応の検討は必要になります。
- 勘合部に関しては、相手部品との寸法が重要になります。製品の寸法は製品設計者により勘合を想定した寸法となっています。コネクタ等の勘合は端子との勘合、製品同士の勘合など重要寸法となります。勘合部分関しては変形及びソリの大きさにより勘合出来ない状態になり為、場合によってはソリ及び変形を想定した金型を製作する必要が出てきます。
ゲートの検討
下の図は四角い製品に肉厚に差をつけて樹脂流動の解析をした結果です。右側の図が製品の形状になります。ひふぁ露側の図は樹脂流動解析の結果になります。肉薄部の中央部分をゲートとして設定したときの結果では、右の肉薄部の充填時間と左に肉厚部では充填時間に大きなさがあることが解ります。
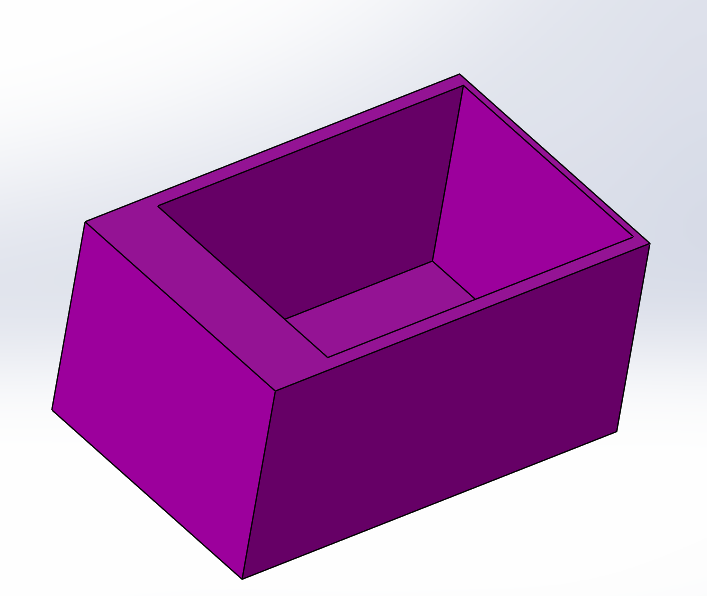
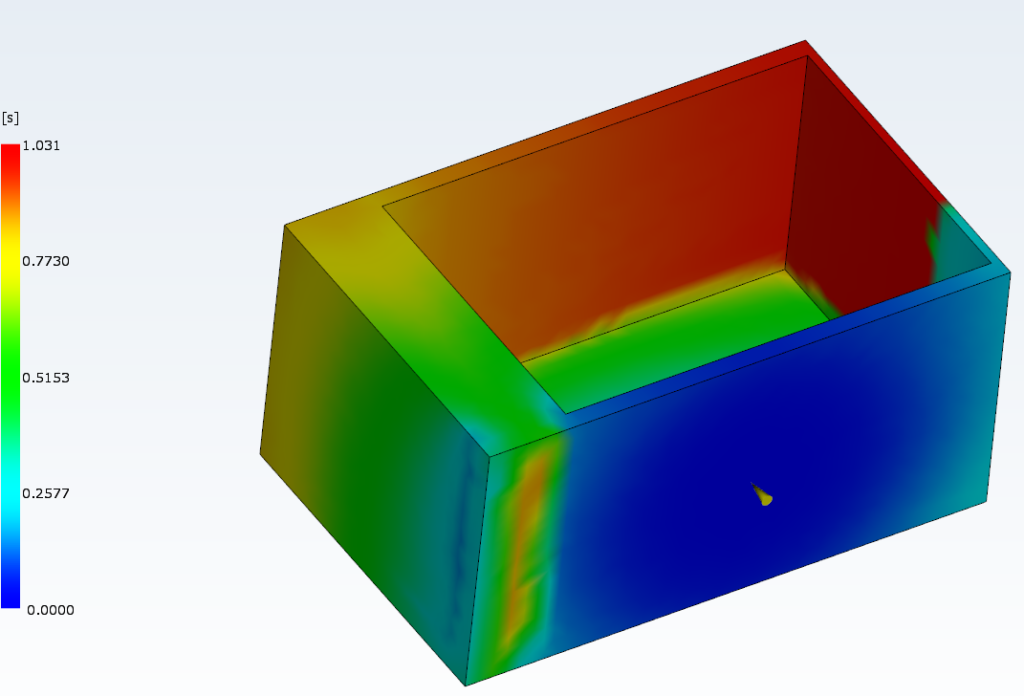
次に充填確実性の結果と品質予測の結果です。左が充填かく実性では肉薄部の合流部分に不安があります。
品質予測に関しては肉厚面全体が黄色の内容で品質不安ありとなります。
充填かっく実性が低い部分に関しては分割検討または、ガス逃げ対策を施しておきましょう。
品質不安部分は肉抜き等必要と思われますが、製品設計者との相談となります。とりあえず最適なゲートの位置を検討して金型設計を進めましょう。
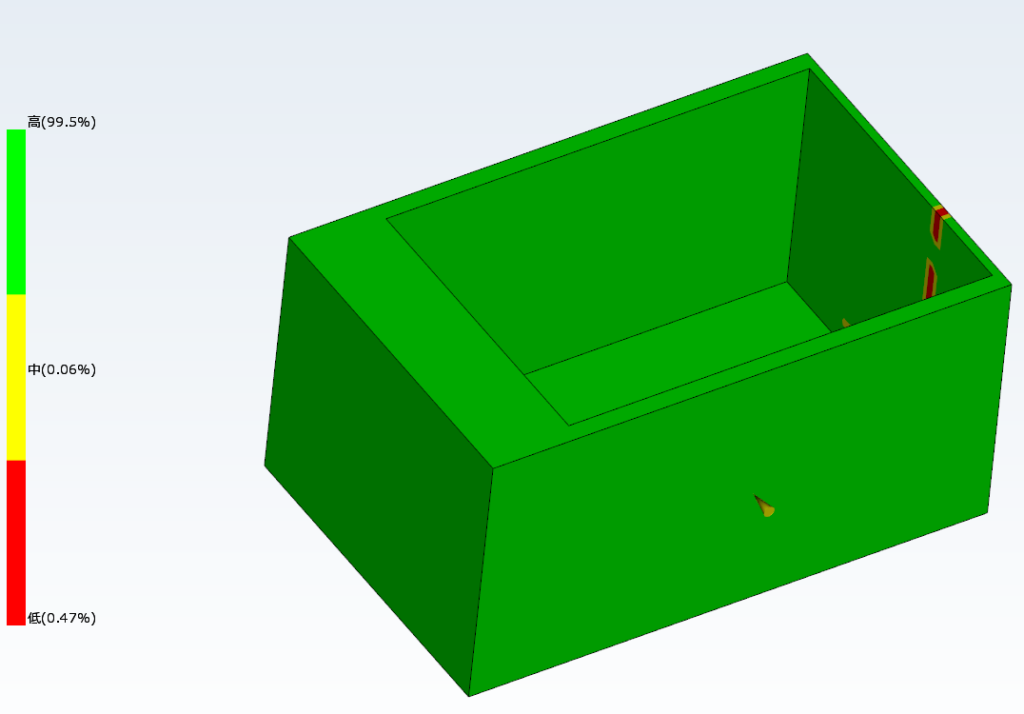
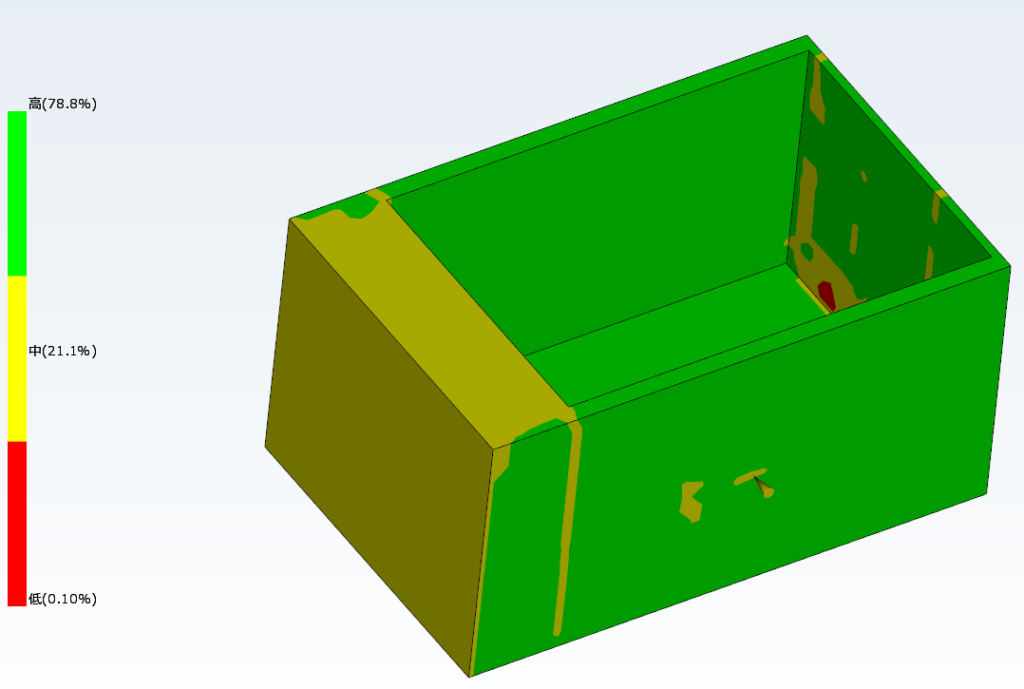
まずは、ゲート位置の変更を検討してみよう。
下に図はゲート位置を肉厚部に変更した結果です。充填時間は大きく違ってきているのが解ります。また、右の図が充填確実性の解析結果ですが充填確実性が上がり充填不安が解消されています。
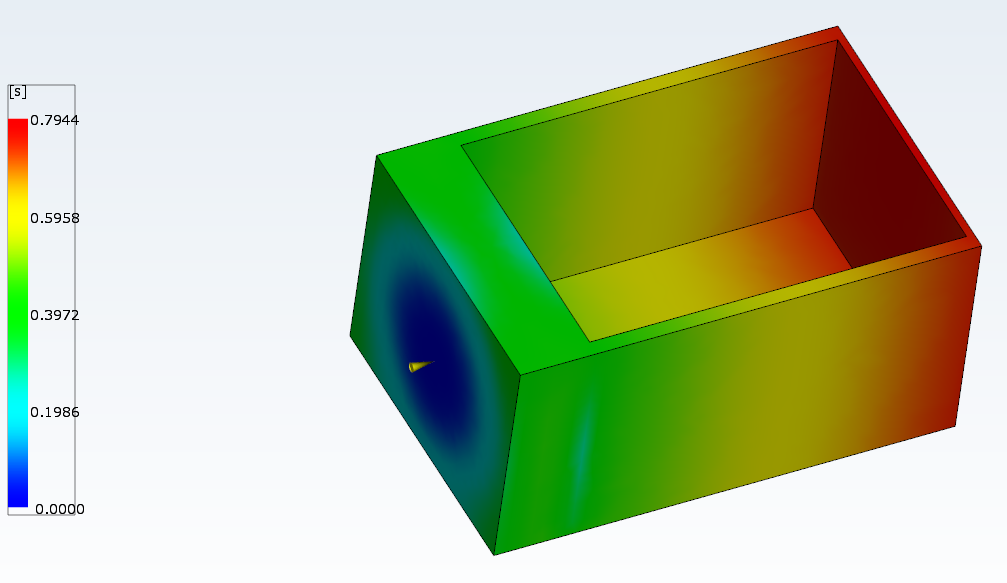
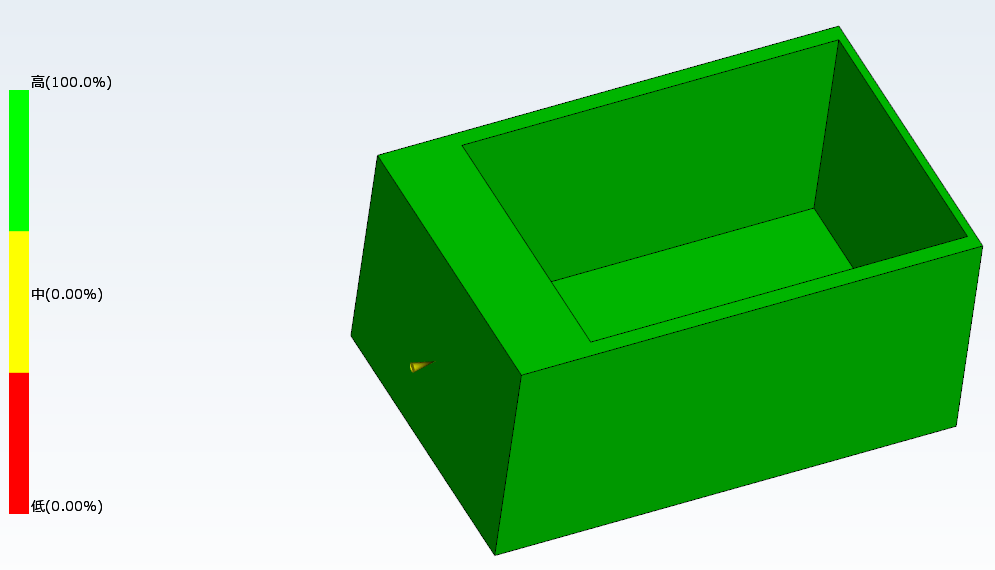
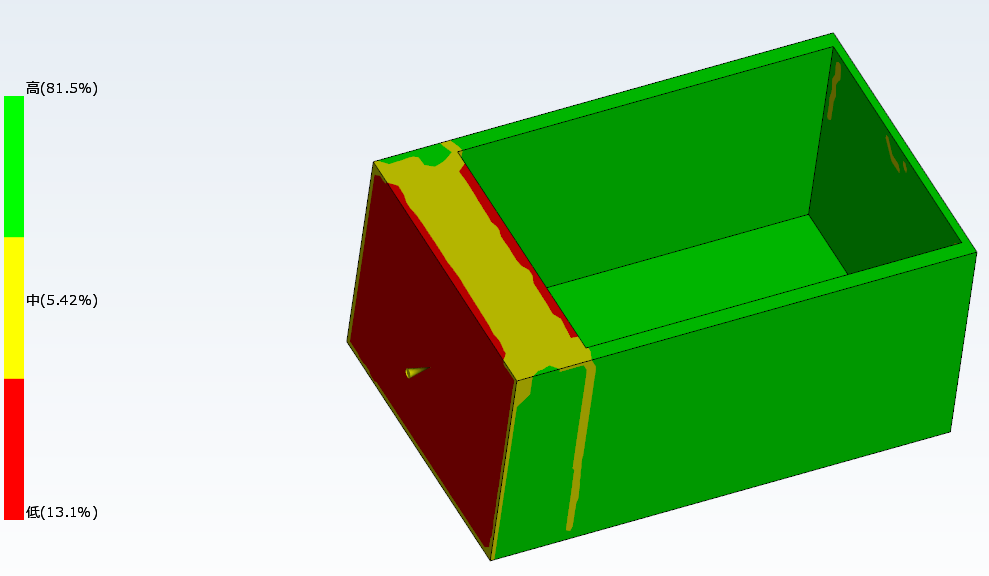
最後に品質予測を確認したが、肉薄部が全面不具合予測が高くなっていいます。
ゲート位置を変える事で充填確実性は上がったが品質予測が悪化しています。
今度は肉薄部から樹脂を注入してみてはどうかと考えられるます。実査にシミレーションしてみよう。
ゲートを肉薄部に変更したが、充填確実性は角部分に一部不案ありで品質予測は肉厚部全体があまり良い結果とはならなかった。
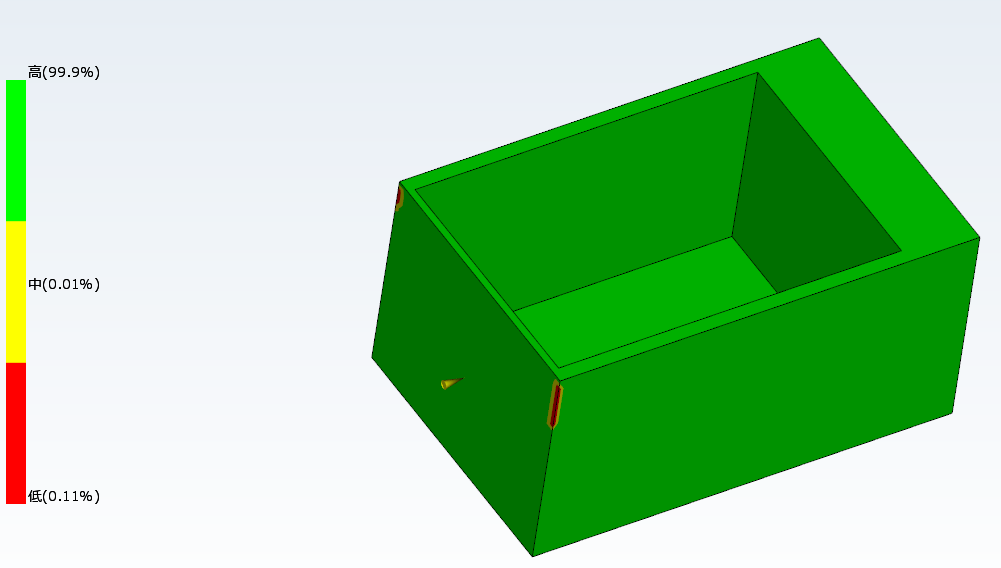
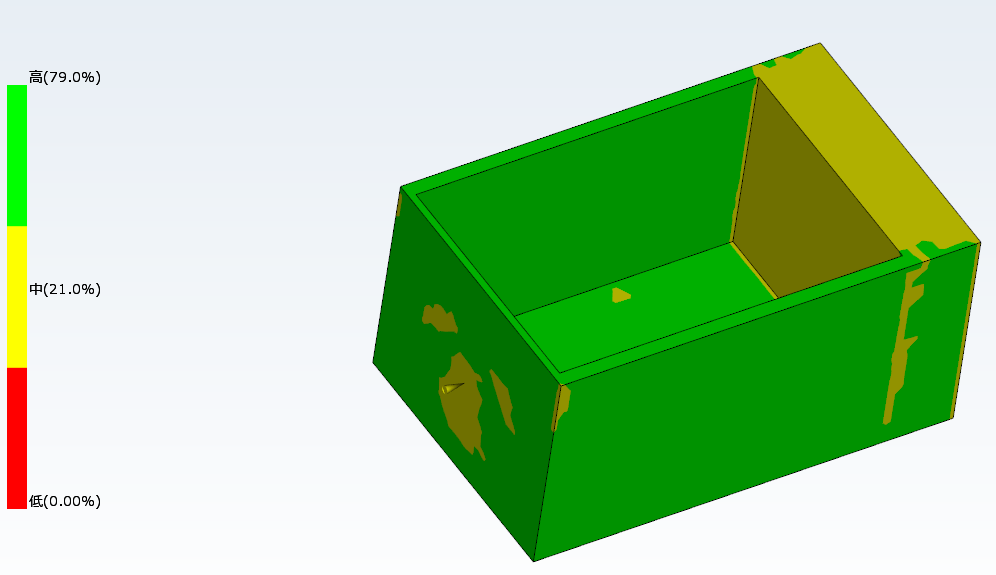
上記の内容からゲートの位置変更により一番赤に内容の少ない肉薄部へのゲートが最適と考えられる。
ただ、ゲートを2か所に設置したり、肉厚部に肉抜き形状を追加することで品質が変わります。
肉厚部に肉盗みを追加した場合の結果を下の図で示します。
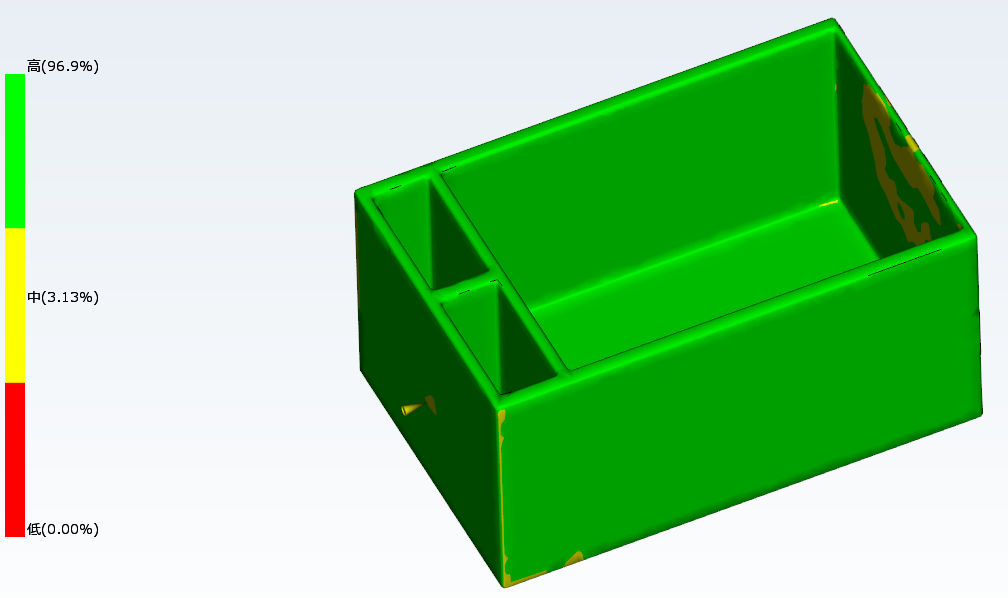
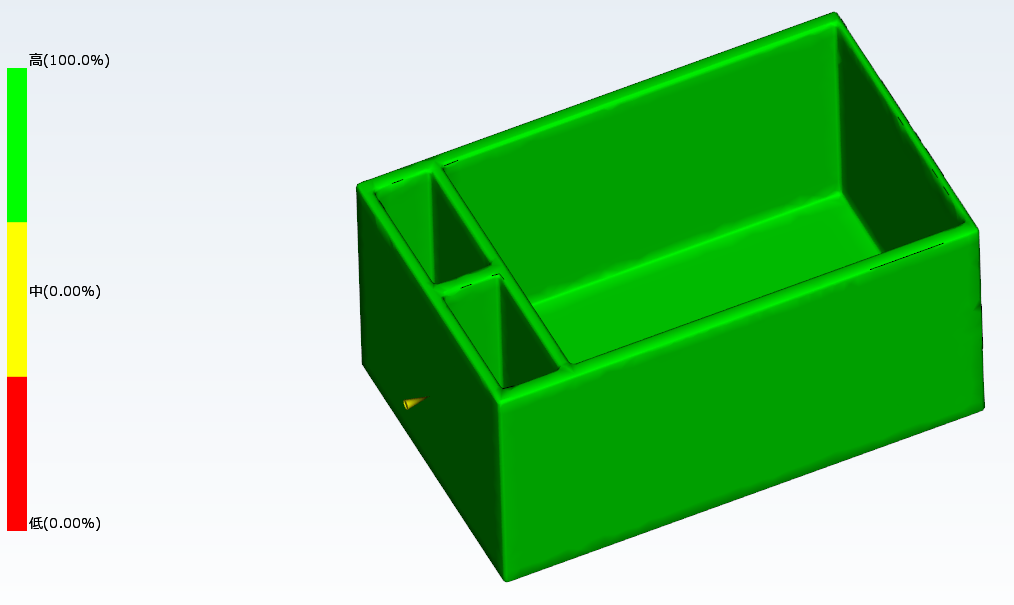
結果として肉盗みを追加することで充填確実性及び品質予測の双方が問題なしとなりました。
ただ、製品形状は製品設計者が検討して作成した形状です。品質の大きく影響する内容が有れば製品設計者と相談してみるのも良品及び歩留まりのない金型製作には必要となる場合もありますのでよく検討してみてください。
製品形状のソリ倒れの予測
ソリとは、製品が熱などの外部要因によって歪む事を指します。
また。コの字形状の製品等は開いている部分が内側に倒れ規格外となります。特に勘合の関する形状及び寸法の場合勘合不具合となり製品の機能を果さないことになります。
正規の製品(ソリ変形無)
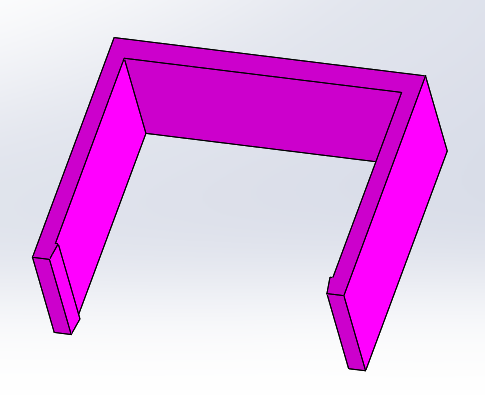
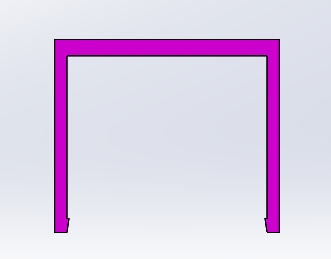
実際の成形品(ソリ変形が発生)

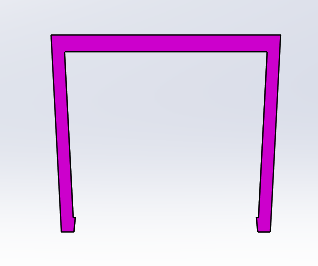
ソリ変形を、見込まないで金型で製品を作成した場合実際成形品を取りだした際に変形して使用出来ないという問題が発生します。
ソリ変形は解析でも検討可能ですが、成形品が解析結果と全く同じになることはほぼないと考えてください。
あくまでも参考目安として解析結果に基づき検討する必要が有ります。
複雑でリスクの高い製品に関しては試作して検討することが最適と考えられます。
類似形状の実績が有れば参考にするのも良いでしょう。
実際に作る金型は変形を見越して変形後に正規の製品形状になるように設定して金型をつくります。
変形を予測した形状
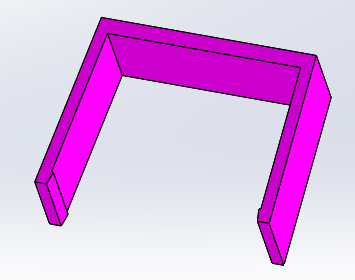
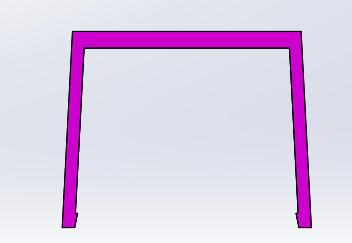
内倒れ変形をする事を想定して外側に製品形状を開いて製品を作るように金型を設計する。
この事から金型設計には解析の結果のほかに試作のデータ及び経験・過去トラ等のデータを参考にして設計する事が重要となります。
収縮図の作成
製品形状に対する検討が終わったら次に収縮図を作成します。製品寸法に対して金型寸法をどの様に設定するか検討します。
まずは、成形材料の特性を材料メーカが出している材料データシートや収縮率情報を基に検討します。
収縮率は流れ方向・直角方向・高さ方向でそれぞれ違ってきます。製品の形状及び大きさ肉厚等から収縮率を設定します。試作を行っていたり類似形状の実績が有れば参考にします。
収縮率が決定したら製品寸法に対して収縮率をかけて金型の製品部寸法を設定します。事前変形及び倒れの懸念がある場合は変形を見越した設定にする、変形予測が想定外になった場合にも部品の追加工で変更できるターゲット寸法としておくことが望ましい。
以前に製作実績が有る場合は基本同様の狙い値で作成する事が望ましい。
(現行品と製品寸法が変わってしまう恐れが有るから。)
分割構想(パーティングライン)
製品モデルが完成したら、金型の分割構想の検討に入ります。
まず最初にパーティングラインを決定します。パーティングラインは基本的にコア側とキャビ側に分ける分割ラインのことです。
基本的にはコア側に製品が貼りついてこなければ、製品を取り出すことが出来ない為必ず製品がコア側に貼りつくように考えて設計をします。
収縮及び製品の食いつき度合いを考慮します。
製品をコア側とキャビ側に分割する際になるべく多くの形状がコア側に来るようにします。
この際に製品を突き出すためのエジェクターピンが設置可能かも合わせて確認します。
外観、外側の部分はキャビ側で形成する様にパーティングラインを決めます。
ただ、製品の形状によっては、コア側の形状が少なくキャビ側に貼りつきそうな場合があります。このような時は製品設計者と相談しコア側にアンダーカットの設置を検討します。またスライドコアを設置してコア側に製品が貼りつくように考慮して設計を行います。
キャビ側に製品が残ってしまうと金型から製品を取り出すことができません。
そのため成形品が作れない成形不可となり金型として成り立たなくなります。
もし、金型製作後のキャビ側に製品残りが発生した際は、キャビ側から製品が取れるようにする為の対策として、
- キャビ側、部品の製品部分の磨き(製品が抜ける抵抗を軽減させる。)
- キャビ側に抜き勾配を設定する。(製品に勾配を付ける事で製品の貼りつきを抑える)
- コア側にアンダーカットの設置。(コア側に製品を引っ張る力を追加してキャビ側の製品を引っ張る)
- スライドコアの追加(スライドコアを追加してコア側に製品を引っ張る力を増大する。大幅ば設計変更が必要となります)
- コア側とキャビ側を逆転させる。(製品が残る形状の方をコア側に変更するエジェクター等の変更もあり大幅な設計変更となります。
以上のことから、最悪でも磨き、抜き勾配の設置、アンダーカットの設置で済むように初期のPL設定が重要になります。
分割構想(部品分割)
パーティングラインが決定したら次に分割の構想はいります。
分割の構想は、以下のことに注意しながら検討する必要があります。
- ガス・ウエルドの発生
樹脂流動を考慮してガス・ウエルドの発生は懸念される部位に関しては分割してガス逃げを設置する必要があります。樹脂流動解析の結果を参考にする事も必要になります。
分割を増やすことにより金型に製作コストは上がりますが、ガス不具合の少ない金型は成形でのメンテナンスサイクルが長くなり成形コストパフォーマンスが高い金型となり最終的にコストパフォーマンスの高い金型となります。 - 分割を増やすことによるデメリット
設計工数・加工部品が増える事で金型の製作コストが上がる。
部品の大きさにによっては、部品強度不足が発生する。
メンテナンスの際の工数が増える。
金型設計者は、分割デメリットも考慮し成形不具合の発生の無い金型を設計する必要があります。
わたし以前経験した金型には製作コストのみを重要視して製作し、立上げまでの時間を要してしまった金型もあります。結果的に分割を追加したり強度対策(樹脂圧対策)を追加したりしてしまい、大幅に製作コストがかかってしまったなどということもありますので分割構想は金型の肝ともいえる作業となります。
概ね分割したい部位が決まったら部品の抜け防止用のツバ・ツバ受け及び組間違いを防ぐための対策誤った場所への組込が出来ない様にします。
組違いの対策は本来の形状と誤った形で製品を製作しにない為に行います。誤った状態で金型を組立て異形状の製品を製作しても使用できません。
誤った製品を市場に流通させてしまえば、大きな問題となります。そのようなことを引き起こさない様にするためにも組間違いの対策は重要な設計ポイントとなります。
ここまでくれば金型の製品を作る部分については概ね完了となります。
ここからは部品図をトレースして部品図を書きます。
ここでは、金型を製作する上での公差設定がとても重要になります。
図面の公差設定
作図作業において重要なポイント公差設定になります。
公差0では加工は出来ません、部品の加工はこの公差のよって許容範囲をきめてその範囲の中で部品を製作します。
公差が多きければ加工の許容範囲が多きい為、加工工数は削減されます。
また、公差が小さければ加工の許容範囲が狭い為、加工者は寸法に気を使わなければいけない為、加工工数は大きくなります。
加工工数のことだけを考えれば公差は大きく設定したほうが、部品加工者への負担は軽減されます。
しかし、公差が大きいと言うことは加工のバラツキが大きくなり組み合わせた際のズレバラツキが大きくなります。
仮に部品外周寸法2mmx4mmの部品に公差±0.01mmの公差設定にした場合最大2.01mmx4.01mm・最小1.99mmx3.99mmとなり最大0.02mmづつの寸法差が発生します。
部品1つだけを見ると寸法差がそれほど大きいと言う認識が無いかもしれません。
しかし金型は1つの部品のみで形成されるわけではない為この寸法差が金型の精度の大きく影響を及ぼします。
例えば寸法差0.02mmの部品が2列5部品づづ並んでいるとします。1列目は最小値の1.99mmx5部品2列目は最大値の2.01mmx5部品を並べた際に1列目は1.99x5=9.95mm2列目は2.01x5=10.05mmになります。
1列目と2列目の寸法差は0.1mmとなり寸法差により隙間が発生します。
仮に公差を±0.001とした場合は右図のように発生したすきまでバリの発生はないと考えられますが、上記設定の公差±0.01の場合は発生したスキマにバリの発生が考えられる為成形は不具合品となる可能性が高い。
公差±0.01の場合
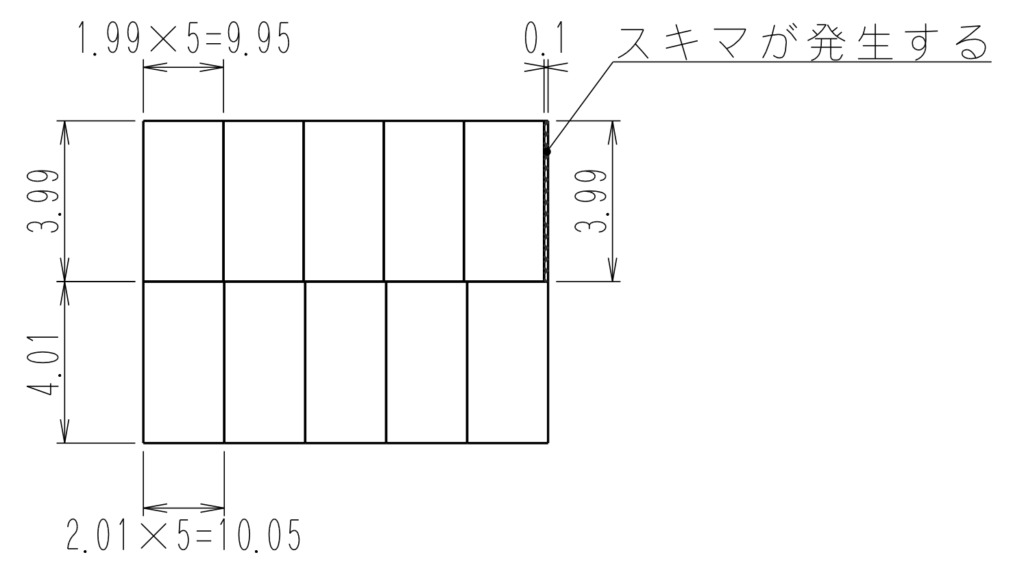
公差±0.001の場合
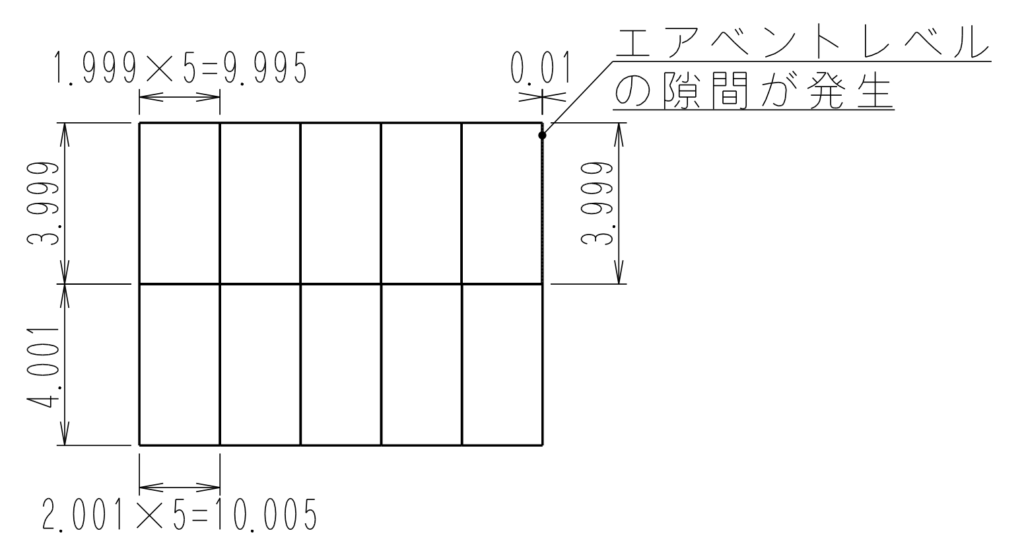
このように単純に並ぶ場合はスキマの発生を予想する事は簡単ですが、金型の場合は多くの部品が複雑に並んでいます。摺合せやクイキリ等合わせ勾配もありスキマの発生を予測するこは難しい為多くの公差は片側公差+0-0.002等と設定する事が多いです。発生するスキマを想定しながら公差を設定する必要があります。
すべての公差を厳しくすればよいのではないかと考えてしまいがちですが、金型自体は基本隙間ばめですので全てを±0で製作しても良い金型は作れませんし±0公差は現実的でないと考えます。
隙間が無ければ型締めでカジリが発生します。コア側とキャビ側・エジェクターピン等適度なスキマが必要です。±0で摺動もしません。
適度なスキマは使用する成形材料等で変わってきますので材料特性を理解し公差の設定をするようにしましょう。
公差のある図面で製作している以上最終的には仕上げ組立工程での調整が必要となってきますので割り切りも必要です。経験を積みながら公差の知見を育てていきましょう。
コメント